
The context
-
A leading automobile player having silo-oriented, directive and selfcentric culture
-
Production processes section target driven, push oriented and intensive batch processing
-
Reactive response to customer feedback, heavy reliance of inspection, and chronic quality problems
-
Organization requiring changes in mindset, behaviors and skills
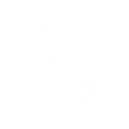
THE SOLUTION
-
Company wide initiative leveraging principles of TQM and lean six sigma launched
-
TEI (Total Employee Involvement), JIT (Just in Time), and TQC (Total Quality Control) to address issues of people, processes and problem-solving holistically
-
All employees trained and engaged on problem solving, and quality championed through reward and recognition

THE IMPACT
-
Radically improved employee engagement scores
-
Continuous Improvement through KAIZEN, and quality a core of new organizational culture and "a way of working"
-
Over 100 chronic problems solved by nearly 50 small groups
-
7 highly successful new products launched (30% of overall product portfolio) within 2 years, aligned with customer voice